Inside A Nicaraguan Cigar Factory
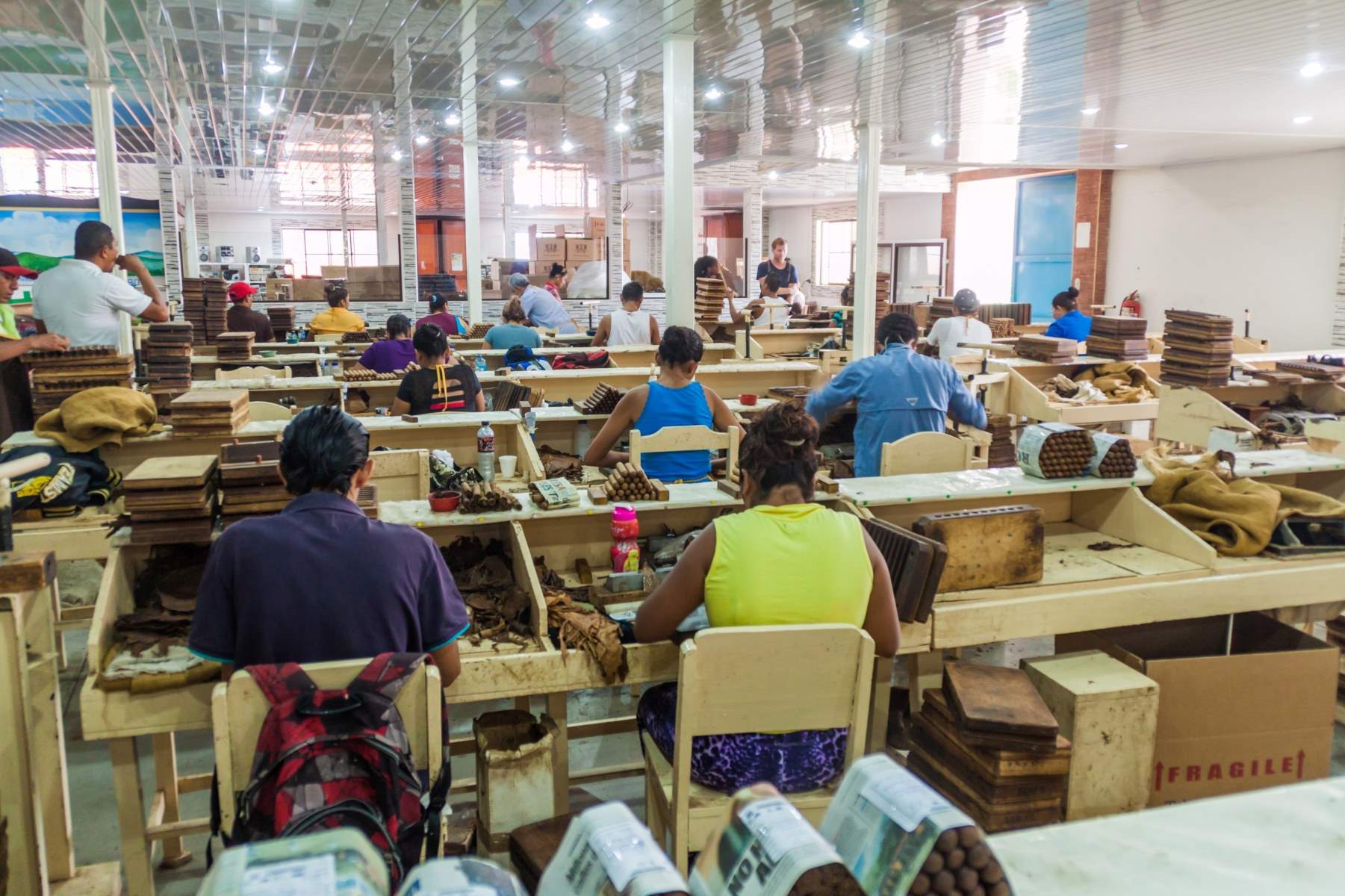
Introduction
Welcome to the fascinating world of Nicaraguan cigars. Steeped in rich history and renowned for their exceptional craftsmanship, Nicaraguan cigars have earned a well-deserved reputation among aficionados around the globe. In this article, we will take you on a journey inside a Nicaraguan cigar factory, where the magic happens and the world’s finest cigars are meticulously crafted.
Nicaragua, located in Central America, is known for its fertile soil and ideal climate, making it the perfect place for growing tobacco. The country’s tobacco industry has flourished over the years, with skilled artisans honing their craft and producing cigars that rival those made in traditional cigar capitals like Cuba and the Dominican Republic. Nicaraguan cigars have become a preferred choice for discerning cigar enthusiasts who appreciate the nuanced flavors and exceptional quality that they offer.
Upon entering a Nicaraguan cigar factory, you are immediately greeted by the alluring aroma of tobacco leaves. The atmosphere is electric, bustling with activity as highly trained rollers delicately work their hands, transforming raw tobacco into exquisite, hand-rolled cigars.
While the process of cigar making may seem straightforward, it is a true art form that requires precision, patience, and expertise. From selecting the finest leaves to blending and rolling, each step is done with utmost care and attention to detail, ensuring that every cigar embodies the mastery and dedication of the skilled artisans.
In the upcoming sections, we will delve into the fascinating history of Nicaraguan cigars, explore the location of a typical cigar factory, and get an in-depth look at the intricate cigar making process. We will also learn about the different types of cigars produced and the rigorous quality control measures put in place to ensure the highest standards. Additionally, we will shed light on the integral role of cigar rollers and examine the work environment within the factory.
While the Nicaraguan cigar industry has seen tremendous success, it has not been without its challenges. We will discuss some of the obstacles faced by the industry and explore the exciting future that lies ahead.
So, get ready to immerse yourself in the captivating world of Nicaraguan cigars as we venture inside a Nicaraguan cigar factory and uncover the secrets behind these exquisite creations.
History of Nicaraguan Cigars
The history of Nicaraguan cigars is deeply intertwined with the country’s rich cultural heritage and its long-standing tradition of tobacco cultivation. While the origins of tobacco in Nicaragua can be traced back to the pre-Columbian era, it was not until the 19th century that the cigar industry began to flourish.
During the colonial period, Nicaragua was under Spanish rule, and tobacco cultivation was primarily for personal consumption. However, with the arrival of German and Cuban migrants in the late 1800s, the commercial production of cigars gained momentum. The expertise brought by these immigrants, combined with the fertile soil and favorable climate of Nicaragua, laid the foundation for the growth of the cigar industry.
One of the key milestones in the history of Nicaraguan cigars was the establishment of the first cigar manufacturer, Joya de Nicaragua, in 1968. This marked a turning point for the industry, as it introduced premium Nicaraguan cigars to the international market. Over the years, Joya de Nicaragua has become synonymous with excellence, producing some of the world’s most sought-after cigars.
In the 1980s, political turmoil in Nicaragua led to a decline in cigar production. However, with stability restored in the 1990s, the industry experienced a renaissance. Cigar enthusiasts began to recognize the unparalleled quality and flavor profiles of Nicaraguan cigars, leading to a surge in demand.
Today, Nicaragua is known as one of the top producers of premium cigars in the world, alongside traditional cigar powerhouses like Cuba and the Dominican Republic. The country’s volcanic soil and tropical climate create optimal conditions for growing tobacco, resulting in an abundance of high-quality leaves.
Nicaraguan cigars have carved a distinctive niche in the market, offering a diverse range of flavors and complexities. The unique combination of Nicaraguan tobacco, known for its earthy and spicy notes, and the expertise of the cigar rollers, results in cigars that satisfy even the most discerning palates.
Furthermore, Nicaragua’s cigar industry has not only gained recognition for its exceptional products but also for its commitment to sustainable practices. Many cigar manufacturers in Nicaragua prioritize environmental conservation and social responsibility, ensuring that the industry remains sustainable and benefits local communities.
The history of Nicaraguan cigars is a testament to the dedication of generations of artisans who have perfected their craft over the years. It is this passion and commitment to excellence that continues to propel the Nicaraguan cigar industry forward, captivating enthusiasts worldwide with the rich flavors and impeccable craftsmanship of their cigars.
Location of the Cigar Factory
A typical Nicaraguan cigar factory can be found nestled in the heart of Nicaragua’s tobacco-growing regions. These regions, such as Estelí, Condega, and Jalapa, are known for their fertile soil, ideal climate, and picturesque landscapes, creating the perfect environment for growing premium tobacco leaves.
Estelí, located in the northern part of Nicaragua, is often referred to as the “Cigar Capital of Nicaragua.” It is home to a significant number of cigar factories, making it a focal point for cigar production in the country. Many top cigar brands have established their manufacturing facilities in Estelí, attracting cigar enthusiasts and industry professionals from around the world.
Condega, situated northwest of Estelí, also plays a significant role in the cigar industry. The region is renowned for producing flavorful tobacco leaves with a unique character. The volcanic soil and microclimate of Condega contribute to the distinctive taste and aroma found in cigars crafted from tobacco grown in this region.
The Jalapa Valley, located in the northernmost part of Nicaragua, is another key area for tobacco cultivation. The region’s higher altitude and cooler climate create conditions that result in tobacco leaves with exceptional flavor complexity. Many cigar manufacturers source their tobacco from Jalapa, ensuring that their cigars deliver a memorable smoking experience.
When visiting a Nicaraguan cigar factory, one can expect to be surrounded by scenic landscapes, vast tobacco fields, and the occasional sight of farmers meticulously tending to the tobacco crops. The proximity to these tobacco-growing regions allows the factories to source high-quality tobacco leaves directly from local farmers, ensuring the freshness and authenticity of their cigars.
While each factory has its distinct character and charm, they share a common dedication to producing cigars of the utmost quality. The factory buildings often blend modern infrastructure with traditional elements, reflecting the merging of old-world craftsmanship and contemporary manufacturing techniques.
For cigar enthusiasts and travelers alike, a visit to a Nicaraguan cigar factory offers a unique opportunity to witness the magical combination of skill, passion, and natural beauty that goes into creating these coveted cigars. It is an immersive experience that provides a deeper appreciation for the artistry and craftsmanship behind every Nicaraguan cigar.
The Cigar Making Process
The process of crafting a Nicaraguan cigar is a meticulous and multi-step journey that requires precision, expertise, and a deep understanding of tobacco leaves. From the selection of the finest leaves to the final touches, each stage in the cigar making process contributes to the creation of a truly exceptional cigar.
1. Tobacco Harvesting: The first step in cigar production is the careful harvesting of the tobacco leaves. Skilled farmers monitor the plants, ensuring that each leaf reaches its optimal maturity before plucking. The leaves are then sorted based on their type, size, and quality.
2. Tobacco Fermentation: After harvesting, the tobacco leaves undergo a fermentation process. The leaves are carefully stacked and bundled in large curing barns, where they undergo controlled fermentation. This process allows the leaves to develop their desired flavors and aromas while reducing bitterness and acidity.
3. Leaf Selection and Blending: Once the fermentation process is complete, master blenders hand-select the best leaves to create the perfect blend for each cigar. They carefully combine leaves from different regions, each contributing unique characteristics to the final product.
4. Rolling: The art of rolling a cigar is perhaps the most iconic and crucial stage of the cigar-making process. Skilled rollers, also known as torcedores, begin by placing the binder leaf, the central layer that holds the filler leaves together, onto a wooden board. They then skillfully add the filler leaves, ensuring an even distribution of tobacco. Finally, they use a delicate wrapper leaf to carefully encase the filler and binder, shaping the cigar into its final form.
5. Aging: After rolling, the cigars enter the aging process. They are placed in specially designed aging rooms, also known as ageing cellars or aging cabinets, where they rest for a designated period. This aging allows the flavors to mingle and harmonize, resulting in a smoother, more refined smoking experience. The length of the aging process can vary, ranging from several months to several years, depending on the desired characteristics of the cigar.
6. Quality Control: Throughout the manufacturing process, rigorous quality control measures are implemented to maintain the highest standards. Qualified inspectors examine each cigar, checking for consistency in construction, appearance, and draw. Only the cigars that meet the strict quality criteria make it to the market, ensuring that aficionados receive a product of exceptional quality.
7. Final Touches: Before the cigars are ready for shipment, they undergo final touches, such as trimming excess tobacco, attaching bands or labels, and ensuring the correct packaging. These finishing touches add the final layer of sophistication to the cigars, ensuring that they are visually appealing and ready to be savored.
The cigar making process is a true labor of love, an intricate dance between nature and human craftsmanship. It is this dedication to perfection and attention to detail that produces the exquisite cigars that Nicaraguan manufacturers are celebrated for.
Types of Cigars Produced
Nicaraguan cigar manufacturers are known for their diverse range of products, catering to a wide spectrum of cigar enthusiasts’ preferences. From mild and creamy to full-bodied and robust, Nicaraguan cigars offer a plethora of options to suit varying tastes. Let’s explore some of the most popular types of cigars produced in Nicaragua:
1. Maduro: Maduro cigars are characterized by their dark, oily wrappers, which develop through an extended fermentation process. These cigars often deliver rich, bold flavors with hints of chocolate, coffee, and earthiness. The Maduro wrappers used in Nicaraguan cigars are renowned for their exceptional quality, adding a layer of complexity to the overall smoking experience.
2. Connecticut: Connecticut cigars feature a smoother, lighter wrapper leaf, often grown in Connecticut, USA, or in Ecuador. These cigars tend to offer a milder smoking experience, with flavors that are more subtle and nuanced. Notes of cedar, cream, and nuts are commonly found in Nicaraguan Connecticut cigars, making them a preferred choice for those seeking a more mild and refined smoke.
3. Habano: Habano cigars are crafted using tobacco leaves from the Habano seed, which originated in Cuba. These cigars are known for their rich, spicy, and full-bodied flavor profiles. Nicaraguan Habano wrappers deliver a unique combination of sweetness and intense earthy notes, making them a favorite among enthusiasts who enjoy cigars with a full flavor spectrum.
4. Ligero Blends: Ligero cigars are made from the leaves harvested from the upper part of tobacco plants, known for their strength and robustness. Nicaraguan ligero blends often feature potent flavors, offering a powerful smoking experience with notes of spice, pepper, and leather. These cigars are sought after by seasoned enthusiasts who appreciate a bolder, more intense smoke.
5. Limited Edition and Boutique Blends: Nicaraguan cigar manufacturers also release limited edition and boutique blends, showcasing their creativity and innovation. These cigars often feature unique combinations of tobacco leaves, aging techniques, and blending methods, resulting in exquisite and exclusive smoking experiences. These limited edition and boutique cigars are highly coveted by enthusiasts and collectors alike.
Regardless of the type, Nicaraguan cigars are revered for their exceptional quality and the attention to detail that goes into their production. The country’s rich tobacco heritage and the skillful blending and craftsmanship result in cigars that offer a vast array of flavors, ensuring that there is a Nicaraguan cigar to suit every preference.
Quality Control Measures
Ensuring consistency and excellence in every cigar is paramount to Nicaraguan cigar manufacturers. As a result, strict quality control measures are implemented at every stage of the production process. Here are some of the key quality control measures in place:
1. Leaf Selection: The process begins with the careful selection of tobacco leaves. Only leaves that meet stringent quality criteria, including size, appearance, and texture, are selected for use in the cigars. Leaves with any imperfections or subpar characteristics are discarded to maintain the highest standards.
2. Rolling Process: During the rolling process, skilled torcedores meticulously examine each cigar, ensuring that it meets the standards set by the manufacturer. They pay close attention to the construction, size, and overall appearance, ensuring consistency across the entire batch of cigars.
3. Draw Testing: To ensure a satisfactory draw, each cigar is carefully tested. This involves using specialized tools or puffing on the cigar to assess the airflow and ensure that it allows for an enjoyable smoking experience. Any cigars with a restricted draw are identified and set aside for further adjustments or rejected.
4. Aging Monitoring: Aging plays a crucial role in enhancing the flavors and overall quality of a cigar. Throughout the aging process, cigars are regularly monitored to ensure that they are maturing properly. Any signs of mold, tobacco beetle infestation, or other issues are promptly addressed to maintain the integrity of the cigars.
5. Flavor Profile Analysis: Cigar manufacturers often conduct sensory evaluations to analyze the flavor profiles of their cigars. Expert testers and blenders assess the taste, strength, aroma, and balance of the cigars to ensure that they align with the desired characteristics. This helps maintain consistency and quality across different batches of cigars.
6. Packaging Inspection: Before the cigars are packaged, the packaging itself is thoroughly inspected. This includes checking for proper labeling, accurate cigar counts, and appropriate packaging materials. Ensuring that the packaging meets quality standards is an essential step to preserve the cigars’ freshness and presentation.
7. Post-production Testing: After the cigars are rolled, aged, and packaged, a final quality control check is conducted. This may include conducting smoke tests, inspecting wrapper appearance, checking for any manufacturing defects, and assessing overall cigar condition. This final step helps identify and eliminate any cigars that may have slipped through earlier quality control measures.
These stringent quality control measures implemented throughout the cigar production process are key to maintaining the exceptional standards that Nicaraguan cigars are known for. By adhering to these measures, manufacturers ensure that every cigar that reaches the hands of enthusiasts is a testament to their commitment to excellence and craftsmanship.
The Role of Cigar Rollers
Cigar rollers, also known as torcedores, play a crucial role in the cigar making process. They are the skilled artisans responsible for transforming raw tobacco into the perfectly rolled cigars we know and love. The art of cigar rolling requires years of training and practice to master, as it demands precision, dexterity, and an understanding of the different tobacco leaves.
A cigar roller’s expertise lies in their ability to handle and manipulate the tobacco leaves with finesse. They carefully select the filler leaves, ensuring the right combination of flavors and strength. These leaves are then arranged in the correct proportion to create a well-balanced cigar. The binder leaf, made from a durable tobacco variety, is skillfully applied to hold the filler leaves together, providing structure and stability.
The delicate wrapper leaf is the final element in the process. Cigar rollers expertly apply the wrapper leaf with great care, using their nimble fingers to ensure a smooth and seamless appearance. The wrapper adds the finishing touch, enhancing the overall aesthetics of the cigar while contributing to its combustion and flavor.
Beyond their technical skills, cigar rollers incorporate their passion and attention to detail into every roll. They are guardians of tradition, preserving the time-honored techniques passed down through generations. Each cigar they produce carries the legacy of their craftsmanship and dedication.
Moreover, cigar rollers serve as custodians of quality control. They meticulously inspect every cigar they roll, ensuring consistent construction, draw, and appearance. They discard any imperfect cigars that do not meet the exacting standards set by the manufacturer. Their keen eye and touch for detail contribute to the overall excellence and reputation of the cigars they produce.
While cigar rolling is a labor-intensive process, it is also a highly valued and respected craft. Many manufacturers recognize the individual contribution of their cigar rollers and acknowledge their skills as integral to their success. Cigar rollers often have their own dedicated stations within the factory, equipped with the tools and materials necessary for their craft.
Today, some cigar manufacturers even offer opportunities for enthusiasts to witness the art of cigar rolling firsthand by providing tours of their factories. These tours offer a unique opportunity to appreciate the skill and artistry of the cigar rollers as they work their magic.
Ultimately, the role of cigar rollers extends beyond the mere act of rolling cigars. They are the keepers of tradition, the guardians of quality, and the artisans who bring each cigar to life. Through their expertise, passion, and commitment to perfection, they ensure that every cigar delivers a supreme smoking experience.
Work Environment in the Factory
The work environment in a Nicaraguan cigar factory is a unique blend of tradition, camaraderie, and focused craftsmanship. Stepping into a bustling factory, you are instantly greeted by the rhythmic sounds of experienced cigar rollers meticulously handcrafting cigars, accompanied by the gentle aroma of tobacco that fills the air.
One notable aspect of the work environment is the strong sense of community and collaboration among the workers. Cigar factories often employ a team of skilled artisans who work together to produce exceptional cigars. This sense of camaraderie fosters a supportive and harmonious atmosphere, creating an ideal setting for creativity and excellence.
The factory floor is typically divided into various sections, with each dedicated to a specific stage of the cigar-making process. Experienced torcedores, often seated at their own workstations, skillfully roll the cigars, while others inspect, apply wrappers, or perform quality control checks.
The workspace of a cigar roller is carefully organized, ensuring easy access to the required tools and materials. At their stations, rollers have access to a selection of tobacco leaves, binder leaves, wrappers, and the necessary instruments such as cutting blades, molds, and humidification systems. This setup allows them to work efficiently and maintain the integrity of each cigar.
Additionally, cigar factories prioritize maintaining optimal humidity and temperature conditions for the tobacco and finished cigars. This is crucial to preserve the flavors, aromas, and overall quality of the cigars. Factories utilize specialized climate control systems to ensure the ideal environment that facilitates the aging, storage, and preservation of the cigars.
Although the work in a cigar factory demands precision and focus, there is often a sense of ease and passion that permeates the atmosphere. Cigar rollers take pride in their craft, and the work environment reflects this passion and dedication. The process of rolling a cigar requires patience, attention to detail, and a true connection with the tobacco leaves, creating a serene atmosphere amidst the busyness of the factory floor.
It is worth noting that some cigar factories also prioritize the well-being of their workers by enforcing strict health and safety measures. These may include proper ventilation systems, protective gear such as gloves and masks, and regular breaks to ensure the physical and mental well-being of the workers.
Overall, the work environment in a Nicaraguan cigar factory embodies a harmonious balance between tradition, camaraderie, and the pursuit of excellence. The shared passion for creating exceptional cigars, combined with a focus on craftsmanship and attention to detail, contributes to the vibrant and inspiring atmosphere that defines the factory floor.
Challenges Faced by the Industry
While the Nicaraguan cigar industry has experienced significant growth and success in recent years, it is not without its fair share of challenges. These challenges often stem from both internal and external factors that impact the production, distribution, and overall viability of the industry.
1. Government Regulations: One of the primary challenges faced by the industry is navigating complex government regulations and policies. Changes in regulations related to tobacco cultivation, manufacturing, and distribution can have significant implications for cigar manufacturers. Compliance with evolving standards and ensuring adherence to strict guidelines adds to the operational complexity and can potentially impact production costs.
2. Trade Restrictions and Tariffs: Trade restrictions and tariffs imposed on tobacco and tobacco products pose challenges for the industry. International trade policies and import/export regulations can increase costs and create barriers to accessing key markets. Fluctuating trade policies can disrupt supply chains and affect the profitability of cigar manufacturers.
3. Climate Change and Natural Disasters: Nicaragua’s vulnerability to climate change and the increasing frequency of extreme weather events pose significant challenges for tobacco cultivation. Droughts, flooding, and hurricanes can damage tobacco crops and interrupt the supply of high-quality tobacco leaves. As a result, cigar manufacturers may face disruptions in production and challenges in maintaining consistent quality.
4. Competition: The cigar industry is highly competitive, with manufacturers from various countries vying for market share. Competition among traditional cigar-producing countries, such as Cuba and the Dominican Republic, can be fierce. Additionally, emerging players in the cigar market create new challenges for Nicaraguan manufacturers seeking to establish and maintain their position in the global market.
5. Business Sustainability: Ensuring the long-term sustainability of the cigar industry requires addressing issues such as labor costs, rising operational expenses, and fluctuations in demand. Maintaining the delicate balance between quality and affordability is essential to meet consumer expectations while ensuring the viability of the industry.
Despite these challenges, the Nicaraguan cigar industry has demonstrated resilience and adaptability. Cigar manufacturers continually strive to overcome these hurdles through innovation, collaboration, and a commitment to producing exceptional cigars that captivate enthusiasts worldwide.
Future of the Nicaraguan Cigar Factory
The future of the Nicaraguan cigar factory is bright and promising, as the country continues to establish itself as a leading player in the global cigar industry. Several factors contribute to the optimistic outlook for Nicaraguan cigars:
1. Rising Popularity: Nicaraguan cigars have gained significant popularity among cigar enthusiasts in recent years. The exceptional quality, diverse flavor profiles, and the artisanal craftsmanship of Nicaraguan cigars have captured the attention of connoisseurs worldwide. As more smokers discover the excellence of Nicaraguan cigars, the demand for these fine cigars is expected to continue growing.
2. Favorable Soil and Climate: Nicaragua’s fertile soil, abundant sunlight, and optimal climate create ideal conditions for tobacco cultivation. The country’s volcanic ash-enriched soil adds unique characteristics to the tobacco leaves, contributing to the rich and complex flavors found in Nicaraguan cigars. These natural advantages provide a strong foundation for continued success in producing exceptional cigars.
3. Innovation and Blending Expertise: Nicaraguan cigar manufacturers are known for their creativity and innovation in blending different tobacco varieties to create unique flavor profiles. By experimenting with new blends and incorporating innovative techniques, they can continue to captivate enthusiasts’ palates and offer exciting smoking experiences. This dedication to continuous improvement ensures that Nicaraguan cigars remain at the forefront of the industry.
4. Sustainable Practices: The commitment to sustainable practices in the cigar industry has gained momentum. Nicaraguan cigar manufacturers recognize the importance of environmental conservation and social responsibility. By implementing sustainable farming practices, supporting local communities, and prioritizing ethical sourcing of tobacco, they contribute to the industry’s long-term sustainability and appeal to discerning consumers who value responsible production.
5. Tourism and Cigar Experiences: Nicaragua’s growing reputation as a premier cigar destination presents opportunities for cigar factories to offer immersive experiences to visitors. Many factories now provide tours, allowing enthusiasts to witness the cigar-making process firsthand and to gain a deeper appreciation for the craftsmanship behind each cigar. This tourism aspect not only boosts the local economy but also raises awareness and appreciation for Nicaraguan cigars globally.
As the Nicaraguan cigar factory evolves and adapts, it is poised to continue carving its place in the global cigar market. The dedication to quality, innovation, sustainability, and the rich tobacco heritage ensures that Nicaraguan cigars will remain highly sought after by both seasoned enthusiasts and newcomers to the world of premium cigars.