How Airplane Wings Work
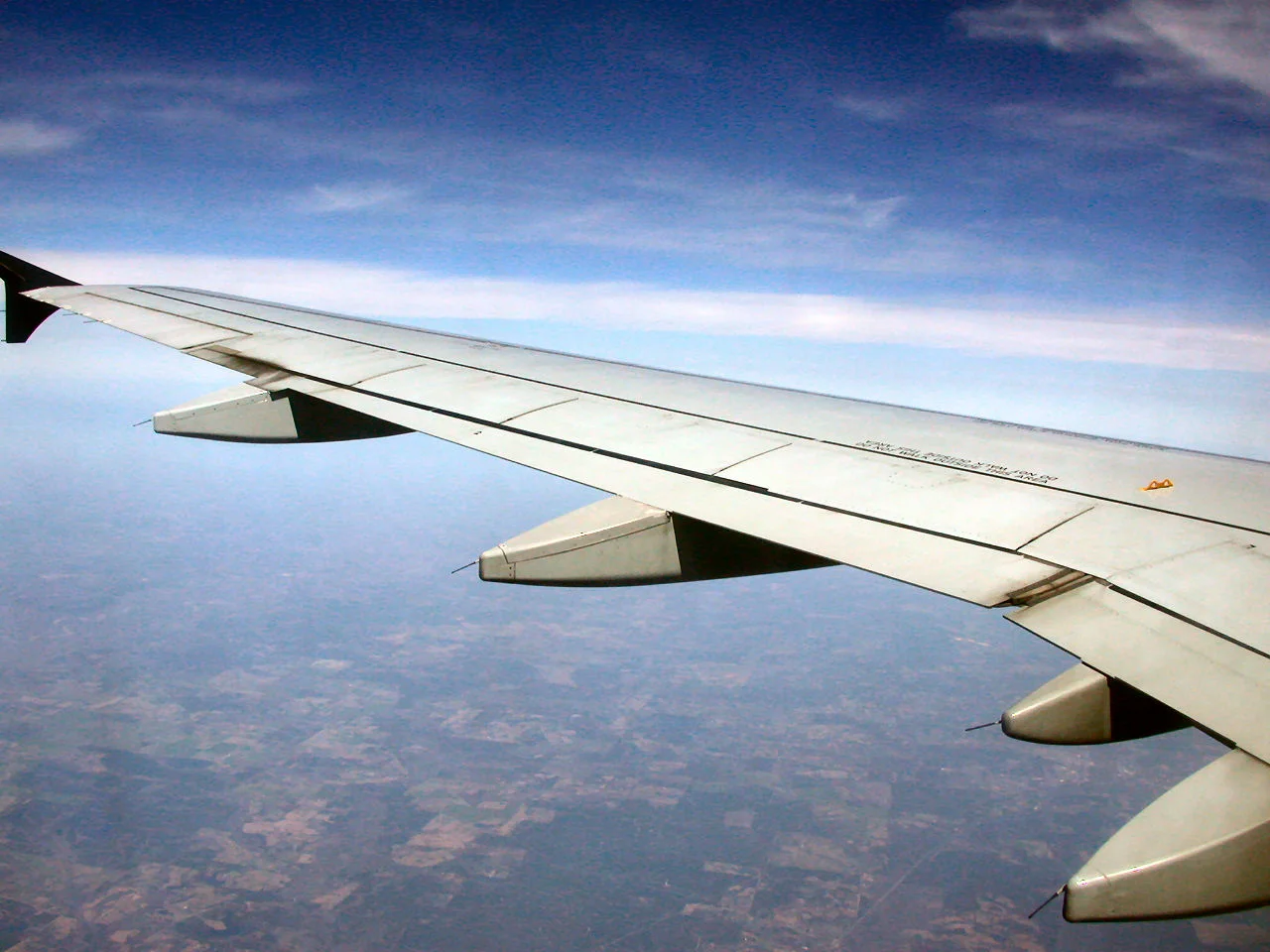
Introduction
When looking at an airplane soaring through the sky, we are mesmerized by its grace and power. Have you ever wondered how these magnificent machines defy gravity and stay suspended in the air? The answer lies in the intricate design and functionality of the airplane wing.
The airplane wing, also known as the wing or the airfoil, is a crucial component of an aircraft. It plays a vital role in generating lift, which enables the plane to take off, stay airborne, and maneuver in the sky. Understanding how airplane wings work is not only fascinating but also essential for anyone interested in the world of aviation.
In this article, we will delve into the basics of aerodynamics, explore the anatomy of an airplane wing, and discuss the different factors that contribute to its efficiency and performance. Whether you’re a seasoned aviation enthusiast or simply curious about the wonders of flight, this article will offer valuable insights into the workings of airplane wings.
To fully grasp the concept of how airplane wings work, we need to have a solid foundation in aerodynamics. Aerodynamics is the study of how objects move through the air and the forces that act upon them. By understanding the principles of aerodynamics, we can gain insight into how airplane wings create lift and control the aircraft’s movement.
At its core, an airplane wing is designed to generate lift by manipulating airflow. The shape, size, and angle of the wing all play a crucial role in achieving optimal lift and reducing drag. Additionally, various wing modifications, such as flaps and spoilers, further enhance the wing’s functionality by allowing for precise control over the aircraft during takeoff, landing, and maneuvering.
The materials and construction methods used for airplane wings have also evolved over the years. Advancements in technology have led to the development of lightweight yet durable wing materials, such as carbon fiber composites, that offer improved fuel efficiency and overall performance.
By the end of this article, you will have a comprehensive understanding of how airplane wings work and an appreciation for the science and engineering behind the incredible feat of human flight. Let’s embark on this journey to uncover the secrets of airplane wings and discover the magic that allows us to conquer the skies.
Basics of Aerodynamics
Aerodynamics is the study of how objects interact with the air around them. When it comes to airplanes, understanding the basic principles of aerodynamics is crucial in comprehending how airplane wings work.
There are four primary forces that act upon an airplane: lift, weight (or gravity), thrust, and drag. Lift is the force that opposes the weight of the aircraft and keeps it aloft. Thrust, generated by the engines, propels the airplane forward. Drag is the resistance that the airplane encounters as it moves through the air.
One of the most fundamental concepts in aerodynamics is Bernoulli’s principle. According to this principle, as the speed of a fluid (in this case, the air) increases, its pressure decreases. When air flows over the curved upper surface of an airplane wing, it has to travel a greater distance compared to the air flowing underneath the wing. This results in faster airflow on top and slower airflow underneath the wing.
Due to Bernoulli’s principle, the faster-moving air on top of the wing has lower pressure compared to the slower-moving air underneath the wing. This pressure difference creates a lifting force. In other words, the asymmetrical shape of the wing allows it to generate lift by creating higher pressure underneath and lower pressure on top.
Another critical factor in aerodynamics is angle of attack. The angle of attack refers to the angle between the wing’s chord line (a line connecting the front and back edges of the wing) and the oncoming airflow. Increasing the angle of attack increases the lift generated by the wing up to a certain point. However, if the angle of attack becomes too high, the airflow over the wing becomes turbulent, resulting in a sudden decrease in lift and increased drag.
These basic principles of aerodynamics lay the foundation for understanding how airplane wings work. By manipulating the shape and angle of the wing, aircraft designers can optimize lift generation, minimize drag, and achieve stable and efficient flight.
Now that we have covered the basics of aerodynamics, let’s dive deeper into the anatomy of an airplane wing and explore its components and functions.
Anatomy of an Airplane Wing
The anatomy of an airplane wing is a complex arrangement of various components working together to generate lift and control the aircraft’s movement. Understanding these components is vital in comprehending the intricacies of how airplane wings work.
The main structural element of a wing is the spar, which runs spanwise, or across the wingspan. The spar provides the necessary strength and rigidity to support the weight of the aircraft and withstand the forces encountered during flight. It is typically made of high-strength materials such as aluminum alloy or composite materials.
Attached to the spar are a series of ribs that run perpendicular to the spar. These ribs not only provide additional structural support but also act as a framework for the skin of the wing. The skin, usually made of aluminum or composite materials, covers the entire wing and helps maintain its shape and streamline airflow.
One of the critical features of an airplane wing is its shape, known as the airfoil. The airfoil is specifically designed to optimize lift generation and minimize drag. It is characterized by a curved upper surface and a flatter or slightly convex lower surface.
The upper surface of the airfoil, known as the camber, is curved to promote the airflow to travel a longer distance, resulting in lower pressure and increased lift. The lower surface, on the other hand, helps maintain the structural integrity of the wing and contributes to the overall lift generation.
Another essential component of the wing is the wingtip or winglet. Located at the outermost edge of the wing, the wingtip helps reduce the formation of vortexes, or swirling air currents, which can increase drag. By mitigating vortex formation, wingtips improve the efficiency and performance of the aircraft.
In addition to the main components, several control surfaces are integral to the functioning of an airplane wing. These control surfaces include flaps and ailerons. Flaps are located on the trailing edge of the wing and can be extended or retracted to modify the shape and surface area of the wing. By extending the flaps during takeoff and landing, the wing’s lift is increased, allowing the aircraft to operate at lower speeds.
Ailerons, on the other hand, are small hinged surfaces attached to the trailing edge of the wing. They work in pairs, with one aileron moving upward while the other moves downward, creating a difference in lift between the two wings. This differential lift allows for roll control and facilitates the bank or turning movement of the aircraft.
Understanding the anatomy of an airplane wing is key to comprehending how it generates lift, minimizes drag, and provides the necessary control for successful flight. In the next section, we will explore the forces at play on an airplane wing and how they contribute to its overall performance.
Lift and Drag
Lift and drag are two fundamental aerodynamic forces that play a crucial role in the operation of an airplane wing. Understanding how these forces interact is essential in grasping the mechanics of how airplane wings work.
Lift is the force that opposes the weight of the aircraft and keeps it aloft. It is generated as a result of the airflow over the wing surface, specifically due to the pressure difference between the upper and lower surfaces of the wing.
As the air flows over the curved upper surface of the wing, its velocity increases, resulting in lower pressure according to Bernoulli’s principle. At the same time, the air flowing underneath the flatter or slightly convex lower surface moves at a slower speed, creating higher pressure.
This pressure difference, or pressure gradient, between the upper and lower surfaces of the wing creates an upward force, known as lift. It is this lift force that allows an aircraft to overcome gravity and achieve flight.
Drag, on the other hand, is the resistance that an aircraft encounters as it moves through the air. It acts in the opposite direction to the motion of the aircraft and is generated by various factors, including the shape of the wing, the viscosity of the air, and the protrusions and imperfections on the surface of the aircraft.
One of the major contributors to drag is called parasite drag, which includes forms such as skin friction drag and form drag. Skin friction drag is caused by the friction between the surface of the aircraft and the air molecules it encounters. Form drag, on the other hand, is a result of the shape and contours of the aircraft that disrupt the smooth flow of air.
Another form of drag is induced drag, which is caused by the production of lift itself. As an aircraft generates lift, it also creates vortexes or swirling air currents at the wingtips. These vortexes contribute to the creation of drag.
To achieve efficient flight, aircraft designers aim to minimize drag while maximizing lift. This is achieved by carefully designing the shape of the wing, as well as incorporating features such as winglets and smooth, streamlined surfaces. By reducing drag, aircraft can fly faster and consume less fuel, resulting in improved performance and efficiency.
Understanding the principles of lift and drag is fundamental to comprehending how airplane wings work. In the next section, we will explore the different wing shapes and designs that optimize these aerodynamic forces for various aircraft configurations.
Wing Shapes and Designs
There is no one-size-fits-all approach when it comes to wing shapes and designs for airplanes. The specific requirements of an aircraft, such as its intended use, speed range, and maneuverability, dictate the optimal wing shape and design. Different wing configurations are carefully designed to enhance aerodynamic performance and to meet the unique needs of different aircraft types.
One common wing shape is the straight wing, which is characterized by a constant chord and a constant angle of incidence along the span of the wing. This simple design provides good low-speed performance and stability, making it suitable for general aviation and slower aircraft.
However, for aircraft that operate at higher speeds and need improved lift and reduced drag, swept wings are commonly used. Swept wings have a backward inclination, or sweep, along the span. This design mitigates the effects of compressibility at high speeds and allows for better supersonic and transonic performance. Swept wings are often found on high-speed commercial jets and military aircraft.
Another type of wing shape is the delta wing, which has a triangular shape. Delta wings are known for their high maneuverability and excellent low-speed performance. They are commonly found on fighter jets and high-performance aircraft.
Some aircraft incorporate a variable-geometry wing, also known as a swing wing. These wings can change their shape during flight, allowing for greater flexibility in different flight conditions. The ability to adjust the wing’s sweep allows for optimal performance across a wide range of speeds. Aircraft such as the F-14 Tomcat and the B-1B Lancer have utilized variable-geometry wings.
Besides shape, the size and aspect ratio of a wing also have a significant impact on its performance. The aspect ratio describes the ratio of the wing’s span to its average chord. Wings with high aspect ratios, such as those found on gliders, offer lower drag and higher lift efficiency but may be less maneuverable at low speeds. Wings with lower aspect ratios are more maneuverable but may have higher drag and reduced lift efficiency.
The design of the wingtip and the inclusion of features like winglets also play a crucial role in improving aerodynamic efficiency. Winglets are small vertical extensions at the wingtips that help reduce drag by minimizing the formation of vortices. They are widely used in modern aircraft to improve fuel efficiency and reduce emissions.
Overall, the selection of wing shape and design is a careful balancing act, taking into account the specific requirements and constraints of the aircraft. By optimizing the wing for the desired performance characteristics, engineers can create aircraft with superior aerodynamic capabilities and enhanced flight performance.
In the next section, we will explore the various types of wing flaps and spoilers that contribute to the control and maneuverability of an aircraft.
Wing Flaps and Spoilers
Wing flaps and spoilers are essential components of an airplane wing that provide additional control and maneuverability during flight. These devices allow the pilot to adjust the wing’s lift, drag, and pitching moment, enhancing the overall performance of the aircraft.
Flaps are movable surfaces installed on the trailing edge of the wing. They can be extended or retracted to modify the wing’s shape and surface area. By extending the flaps, the curvature and surface area of the wing increase, resulting in increased lift generation. This is particularly beneficial during takeoff and landing, when the aircraft needs to operate at lower speeds and maintain sufficient lift to stay airborne.
There are several types of flaps commonly used in aircraft. Plain flaps extend straight down from the trailing edge of the wing and are effective in increasing lift but also increase drag. Split flaps, on the other hand, are hinged at the bottom of the wing and when extended, they increase both lift and drag. Slotted flaps, which have a slot between the wing and the flap, allow for better airflow over the top surface and increase lift without a significant increase in drag. Finally, there are also complex flaps, such as Fowler flaps, that extend backward and downward, increasing both lift and wing surface area.
Spoilers, on the other hand, are used primarily for reducing lift and increasing drag. These are panels that can be raised on the upper surface of the wing, disrupting the smooth airflow and reducing the amount of lift being produced. Spoilers are commonly used during landing to decrease lift and aid in descent. They are also used during certain flight conditions to improve stability and control.
One important use of spoilers is in the implementation of the spoilerons control system. In this system, the spoilers act as both spoilers and ailerons, providing roll control by raising or lowering on one side of the wing while the opposite side remains stationary. This asymmetric deployment creates differential lift and allows for precise banking and turning of the aircraft.
Both flaps and spoilers contribute to the overall controllability and maneuverability of the aircraft. By adjusting the position of these devices, pilots can optimize the lift, drag, and stability of the wing, enabling smooth takeoffs, landings, and efficient flight performance.
Now that we have explored the various components and features of an airplane wing, let’s dive into the materials and construction methods used to create these remarkable structures in the next section.
Wing Materials and Construction
The materials and construction methods used for airplane wings have evolved significantly over the years, driven by advancements in engineering and technology. The goal is to create wings that are not only strong and durable but also lightweight, fuel-efficient, and aerodynamically optimized.
Traditionally, wings were constructed using aluminum alloys, which offer a good balance of strength, weight, and cost. Aluminum wings are relatively easy to manufacture and repair, making them a popular choice for many aircraft. However, as the aviation industry continues to strive for improved fuel efficiency, newer materials have emerged.
One of the most significant advancements in wing materials is the use of composite materials, such as carbon fiber reinforced polymers (CFRP). These materials consist of carbon fibers embedded in a matrix, typically epoxy resin. CFRP offers exceptional strength-to-weight ratio, corrosion resistance, and fatigue resistance.
The use of composite materials allows for greater design flexibility, as they can be molded into complex shapes that optimize aerodynamic performance. Unlike metal wings, composite wings have a smooth surface, reducing drag and enhancing fuel efficiency.
In addition to the material itself, the wing’s construction method is also crucial. Wings are typically constructed using a combination of structural components like spars and ribs, with the skin covering the entire structure. With the advent of composite materials, advanced manufacturing techniques, such as automated layup and resin infusion, are employed to ensure precise and consistent fabrication.
Composite wings are built in a process called “layup,” where layers of carbon fiber fabric are placed in a mold and impregnated with resin. This creates a strong, lightweight, and seamless structure. The use of advanced adhesives allows for the bonding of various components, reducing the need for mechanical fasteners and further enhancing the wing’s strength and integrity.
Another aspect of wing construction is the integration of fuel storage. In many aircraft, the wings house fuel tanks, which need to be carefully designed and constructed to ensure safe storage and distribution of fuel. The wing’s structural elements must be capable of supporting the weight of the fuel and accommodating the necessary plumbing and access points.
Overall, the choice of wing materials and construction methods is a carefully considered decision to meet the specific requirements of an aircraft. Whether it’s the use of traditional aluminum alloys or the adoption of advanced composite materials, the ultimate goal is to create wings that offer optimal performance, efficiency, and safety.
Having explored the materials and construction of airplane wings, let’s now delve into the concept of wing efficiency and its impact on the overall performance of an aircraft in the next section.
Wing Efficiency and Performance
The efficiency and performance of an airplane wing are critical factors in determining the overall capabilities of an aircraft. A well-designed wing can contribute to enhanced fuel efficiency, increased lift, reduced drag, and improved stability and control.
One measure of wing efficiency is its lift-to-drag ratio (L/D ratio). The L/D ratio indicates the amount of lift generated by an airplane wing in comparison to the amount of drag it produces. Higher L/D ratios indicate more efficient wings that can generate a greater amount of lift while minimizing drag.
To achieve high L/D ratios, wing designers focus on reducing drag. This can be accomplished through aerodynamic shaping, careful control of airflow, and the use of features like smooth surfaces, streamlined wingtips, and optimized wing sections.
Efficient wings are also designed to minimize induced drag. Induced drag is produced as a byproduct of generating lift and is inherently present in any wing design. Its reduction involves minimizing wingtip vortices, which are the swirling air currents that form at the wingtips. The use of winglets or other devices helps mitigate these vortices, reducing induced drag and improving efficiency.
Aircraft wings are also designed for specific purposes, such as low-speed capabilities, high-speed performance, or maneuverability. For example, wings with high camber and large surface area are more suitable for slower flight regimes, allowing for greater lift at lower speeds. Conversely, wings with reduced camber and higher sweep angles are optimized for high-speed flight, reducing drag and maintaining stability.
The structural strength and integrity of the wing are also essential for performance. A well-constructed wing can withstand the forces encountered during flight, such as aerodynamic loads and turbulence. Strong spars, ribs, and skin contribute to structural integrity and reliability, ensuring safe and optimal flight operations.
Efficiency and performance are not only crucial for commercial aircraft but also for general aviation and other specialized aircraft. In the case of electric or hybrid-electric aircraft, efficiency becomes even more significant as these aircraft strive for increased range and reduced energy consumption.
In recent years, advancements in wing design, materials, and manufacturing techniques have significantly contributed to improved wing efficiency and performance. The use of composite materials, advanced aerodynamic modeling, and computer-aided design (CAD) tools allow for more precise and optimal wing shapes, resulting in enhanced aerodynamic performance.
Ultimately, the efficiency and performance of an airplane wing are integral to the success and abilities of an aircraft. Through continuous research and development, engineers strive to create wings that offer optimal lift, reduced drag, and improved overall flight characteristics.
Now that we have explored the various aspects of wing efficiency and performance, let’s conclude our journey by summarizing the key insights gained from understanding how airplane wings work.
Conclusion
Understanding how airplane wings work provides us with a fascinating insight into the world of aviation. From the basic principles of aerodynamics to the intricate design and construction of wings, we have explored the key factors that contribute to their efficiency and performance.
Airplane wings are masterpieces of engineering, designed to generate lift and overcome drag, enabling aircraft to take flight and maneuver through the skies. The shape, size, and angle of the wing, as well as the inclusion of features like flaps, spoilers, and winglets, all play a crucial role in optimizing aerodynamic forces to achieve optimal lift and controlled flight.
The materials used in wing construction have evolved, with the advent of composite materials providing lightweight, durable, and aerodynamically superior options. Advanced manufacturing techniques ensure precise fabrication, while the integration of fuel storage and fuel efficiency considerations contribute to holistic wing design.
An efficient and well-designed wing can enhance fuel efficiency, increase lift, reduce drag, and improve stability and control. The goal is to achieve high lift-to-drag ratios, minimize induced drag, and tailor wings to specific flight regimes and aircraft requirements.
Through continuous research and development, engineers continue to refine and innovate in the field of wing design, seeking to unlock greater efficiency, better performance, and improved flight capabilities. The quest for more sustainable and eco-friendly aviation also drives advancements in wing technology as wings play a significant role in reducing fuel consumption and emissions.
By understanding the fundamentals of how airplane wings work, we gain a deeper appreciation for the technological marvels that enable us to conquer the skies. Whether it’s the straight-winged aircraft for general aviation, high-speed swept-wing jets, or maneuverable delta-winged fighters, each design is optimized to meet specific performance requirements.
So the next time you gaze at an airplane soaring through the sky, take a moment to marvel at the wing that enables its flight. The combination of science, engineering, and ingenuity showcased in the wings of an aircraft is truly a testament to the remarkable capabilities of human innovation.