How To Design An Airplane
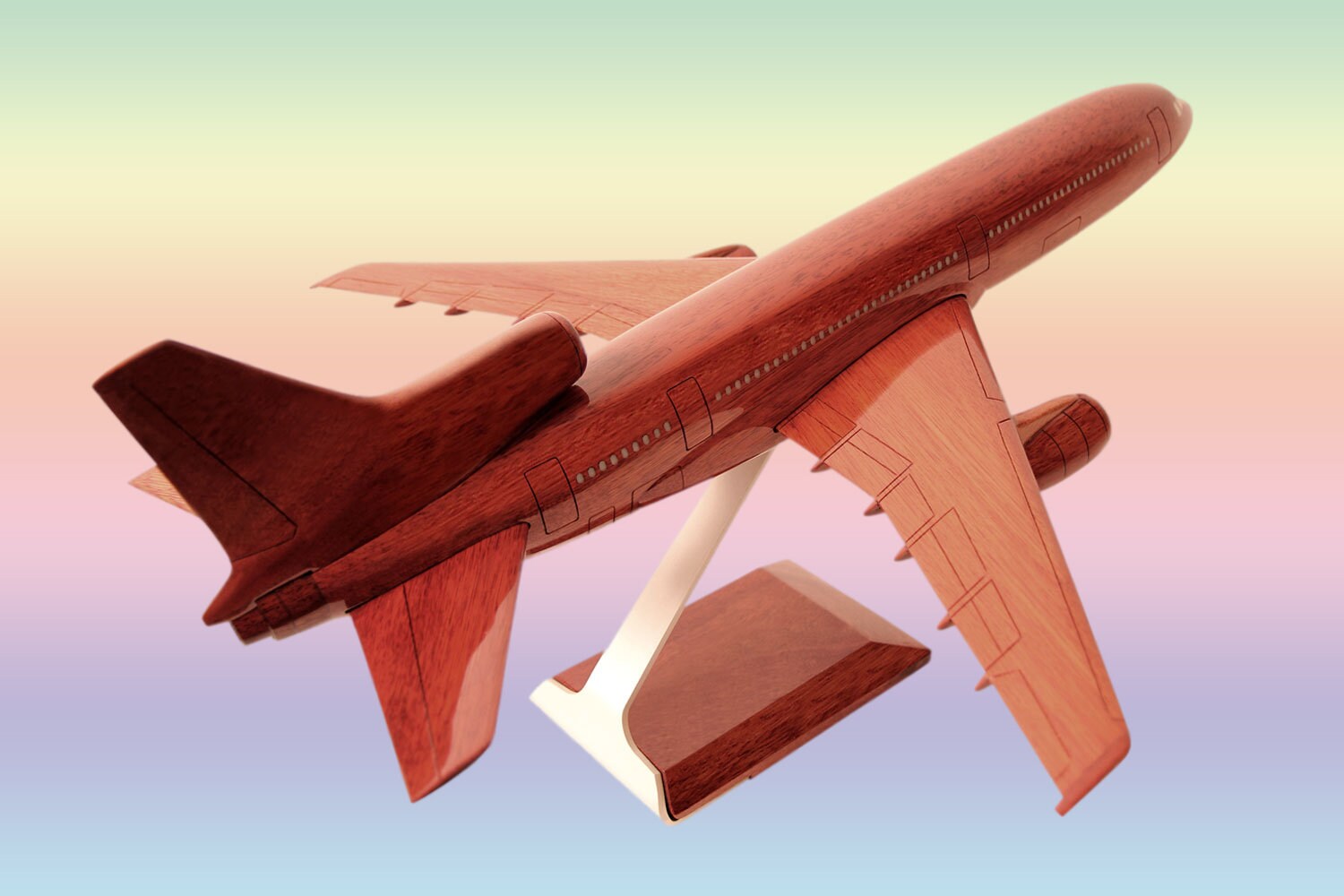
Introduction
Welcome to the world of airplane design! Designing an airplane is a fascinating and complex process that requires a deep understanding of aerodynamics, engineering principles, and safety regulations. Whether you’re an aviation enthusiast or an aerospace engineer, this article will guide you through the essential steps involved in designing an airplane.
Creating an aircraft involves a meticulous blend of creativity, engineering expertise, and attention to detail. Each design decision can have a significant impact on the performance, structural integrity, and overall functionality of the airplane. From defining the design objectives to conducting research, conceptualizing the aircraft, and implementing safety features, every stage requires careful consideration.
Throughout this article, we will explore the step-by-step process of designing an airplane. We will delve into the key aspects, including aerodynamics, structural design, materials selection, wing configuration, and safety features. By following these steps, you can create a well-designed aircraft that meets the requirements and expectations of modern aviation.
It’s important to note that designing an airplane is a collaborative effort that involves a multidisciplinary team of engineers, aerodynamicists, designers, and technicians. Their expertise and combined efforts are crucial in achieving a successful and efficient aircraft design.
So, whether you have dreams of designing the next generation of passenger planes or simply want to gain a deeper understanding of the intricate process behind aviation, let’s embark on this exciting journey of airplane design together.
Step 1: Define the Design Objectives
Before diving into the intricacies of airplane design, it is crucial to start by defining the design objectives. This step lays the foundation for the entire design process and helps identify the purpose, performance requirements, and target audience of the airplane.
The design objectives of an airplane can vary greatly depending on its intended use. For example, a commercial airliner will have different objectives compared to a military fighter jet or a small recreational aircraft. Some common design objectives may include:
- Performance: Determine the desired flight characteristics such as speed, range, payload capacity, and fuel efficiency. This will influence decisions related to engine selection, wing configuration, and aerodynamic design.
- Safety: Ensure that the aircraft meets all regulatory safety standards and includes necessary features such as emergency exits, fire suppression systems, and crashworthy structures.
- Comfort: Consider passenger comfort by designing a spacious cabin layout, comfortable seating, adequate storage space, and noise reduction measures.
- Functionality: Define the aircraft’s intended capabilities and features, such as cargo handling, medical evacuation, surveillance, or aerial photography.
- Cost-effectiveness: Balance the performance requirements with cost considerations to design an aircraft that is economically viable to manufacture, operate, and maintain.
It is essential to involve stakeholders, such as the client, operators, and end-users, in the process of defining the design objectives. Their input and feedback will help ensure that the final aircraft design meets their specific needs and expectations.
Once the design objectives are clearly defined, they will serve as a roadmap for the entire design process. They provide a clear direction and help prioritize design decisions, ensuring that the end result aligns with the initial goals.
Remember, the design objectives may evolve throughout the design process as new information is obtained and requirements change. Flexibility and adaptability are essential to create an aircraft design that successfully meets the desired objectives.
Step 2: Conduct Research and Analysis
Once the design objectives are established, the next step is to conduct thorough research and analysis. This step is critical in ensuring that the design is based on sound engineering principles, industry best practices, and the latest technological advancements.
Research involves studying existing aircraft designs, analyzing their performance characteristics, and identifying areas for improvement. This includes examining the aerodynamics, structural integrity, materials used, and overall efficiency of similar aircraft in the market. By understanding what works and what doesn’t, you can make informed design decisions and avoid repeating past mistakes.
An important aspect of the research phase is analyzing the operating conditions and environmental factors that the aircraft will encounter. Factors such as altitude, temperature, humidity, and wind patterns can greatly influence the performance and design considerations. This analysis will help determine the appropriate specifications and requirements for the aircraft.
Computer-aided design (CAD) software and simulation tools play a significant role during this stage. Using these tools, engineers can model and simulate various aspects of the aircraft, including aerodynamics, stress analysis, and performance characteristics. By running simulations, designers can evaluate different design options and make data-driven decisions.
Another important aspect of research and analysis is conducting market research. This involves understanding the current market trends, customer demands, and competition. Identifying the needs and preferences of potential customers will help guide the design process and ensure the aircraft meets market demands.
Additionally, researching and analyzing the regulatory requirements and certification standards is vital to ensure that the aircraft design complies with industry regulations and safety standards. This includes considering factors such as weight restrictions, fuel efficiency, noise levels, and emissions control.
It’s important to note that research and analysis are ongoing processes throughout the design phase. As new information becomes available, adjustments and refinements may be necessary. By staying up-to-date with the latest advancements and industry developments, you can ensure that your aircraft design is innovative, efficient, and safe.
Step 3: Conceptualize the Aircraft Design
With the research and analysis phase complete, the next step is to conceptualize the aircraft design. This is where creativity and innovation come into play, as you develop the initial ideas and visualizations for the aircraft.
During this stage, it’s important to consider the overall form and aesthetics of the aircraft. Factors such as the fuselage shape, wing configuration, tail design, and overall proportions are key elements in the visual appeal as well as the aerodynamic performance of the aircraft.
Sketching and 3D modeling software are valuable tools in this phase, allowing you to explore different design options and refine your ideas. This includes experimenting with various wing shapes, tail configurations, and fuselage profiles.
Additionally, you need to consider the cockpit design and arrangement. This involves determining the placement and ergonomics of controls, instrument panels, and display systems to ensure optimal visibility and usability for the pilots.
During the conceptualization phase, it’s also important to consider the target audience and their specific needs. For example, if the aircraft is meant for short-haul flights, comfort and convenience for passengers may be a higher priority. On the other hand, if the aircraft is designed for cargo transportation, payload capacity and efficient loading and unloading systems would be crucial considerations.
As you conceptualize the aircraft design, keep in mind the performance objectives defined earlier. Strive to create a design that maximizes speed, range, fuel efficiency, and overall operational capabilities.
Throughout this stage, collaboration and feedback from the design team, engineers, and other stakeholders are essential. This ensures that the design aligns with the initial objectives and that any potential challenges or limitations are addressed early in the process.
Remember, the conceptualization phase is the initial step in transforming ideas into a tangible design. It is a stage where creativity flourishes, pushing the boundaries of innovation and setting the foundation for the detailed design work that follows.
Step 4: Plan the Aircraft Layout
In step 4 of the aircraft design process, the focus shifts to planning the layout of the aircraft. This involves determining the arrangement and organization of various components, systems, and functionalities within the aircraft.
One of the key elements to consider is the seating arrangement, especially for commercial aircraft. Factors such as passenger capacity, seating comfort, and ergonomics must be taken into account. Ensuring adequate legroom, seat width, and accessibility for passengers with disabilities are important aspects of creating a comfortable and accommodating cabin space.
Alongside the seating layout, careful consideration must be given to the placement of amenities such as lavatories, galley areas, and storage compartments. These spaces should be strategically integrated to provide convenience and functionality for passengers and crew members.
The location of crucial systems and components, such as fuel tanks, electrical systems, and avionics, also needs to be accounted for in the aircraft layout. Placing these elements in appropriate positions ensures ease of access for maintenance and minimizes the impact on the overall balance and weight distribution of the aircraft.
Additionally, the layout should take into consideration the flow of passengers and crew members throughout the aircraft. Ensuring clear and efficient pathways, emergency exit placements, and accessibility for emergency personnel are essential for passenger safety.
During the layout planning stage, it’s important to coordinate and communicate with various stakeholders, including engineers, interior designers, and operational experts. Their expertise will help guide the design decisions and optimize the efficiency, functionality, and safety of the aircraft interior.
Using CAD software, designers can create detailed 2D and 3D models of the aircraft layout, allowing for a comprehensive visualization and evaluation of the design. This enables the identification of potential design issues or conflicts early in the process, saving time and resources in the long run.
By thoughtfully planning and organizing the layout, you can create an aircraft that provides a harmonious blend of comfort, functionality, and efficiency for passengers and crew members alike.
Step 5: Focus on Aerodynamics
In the aircraft design process, step 5 revolves around focusing on aerodynamics. Aerodynamics plays a vital role in the performance, efficiency, and safety of the aircraft.
At this stage, designers must carefully consider the shape and configuration of the aircraft’s wings, fuselage, and other aerodynamic surfaces. The goal is to minimize drag, enhance lift, and optimize airflow around the aircraft.
One key factor to consider is the wing design. The shape, size, and angle of attack of the wings greatly influence the lift and stability of the aircraft. High-performance aircraft often feature wings with advanced aerodynamic profiles, such as swept-back or delta wings, to increase their efficiency and maneuverability.
In addition to the wings, the fuselage design also plays a crucial role in aerodynamics. A streamlined and properly-shaped fuselage helps reduce drag and allows for efficient flow of air around the aircraft. Considerations such as cross-sectional area, tapering, and minimizing surface imperfections contribute to improved aerodynamic performance.
The placement and design of control surfaces, such as the tailplane, elevators, and rudder, are also important for stability and control. These surfaces help in maintaining balance, stability, and maneuverability during flight.
To analyze the aerodynamic performance of the aircraft, engineers often employ computational fluid dynamics (CFD) simulations. These simulations provide valuable insights into how the airflow interacts with the aircraft’s surfaces, allowing designers to optimize the design for efficient flight.
Throughout the aerodynamic design process, considerations of weight, balance, and structural integrity are important. The placement of components, such as engines, fuel tanks, and landing gear, must be carefully integrated into the overall aerodynamic design to minimize drag and maintain stability.
It is important to note that aerodynamics and structural design are closely intertwined. The structural integrity of the aircraft must be able to withstand the forces and loads imposed by aerodynamic forces. Collaboration between aerodynamicists and structural engineers is essential to strike the right balance between aerodynamic efficiency and structural integrity.
By focusing on aerodynamics during the aircraft design process, engineers can optimize the performance, efficiency, and overall flight characteristics of the aircraft. A well-designed aerodynamic profile not only contributes to fuel efficiency but also enhances stability, control, and passenger comfort.
Step 6: Determine the Structural Design
In the aircraft design process, step 6 involves determining the structural design of the aircraft. This step focuses on creating a robust and reliable structure that can withstand the forces and loads encountered during flight.
The structural design considers the materials, construction methods, and overall framework of the aircraft. It ensures that the aircraft is strong, lightweight, and capable of withstanding various flight conditions, including turbulence, takeoff and landing forces, and structural stresses.
One of the key considerations in structural design is material selection. Engineers must choose materials that possess high strength-to-weight ratios, durability, and resistance to corrosion. Common materials used in aircraft construction include aluminum alloys, composite materials, and titanium alloys.
Another critical aspect is the overall framework of the aircraft, which provides structural support and maintains the shape and integrity of the aircraft. The framework includes the fuselage, wings, tail, and structural components such as spars, ribs, and stringers. The design must ensure that these components are properly sized, reinforced, and integrated to provide optimal structural strength.
Computer-aided design (CAD) software is commonly used in structural design to create accurate 3D models of the aircraft’s structure. These models allow engineers to analyze stress, strain, and load distribution, ensuring that the structure can withstand anticipated forces without compromising safety or performance.
Furthermore, structural design also takes into account factors such as fatigue life, vibration resistance, and impact resilience. Ensuring that the structure can withstand prolonged use, harsh environments, and unforeseen events is crucial for the aircraft’s longevity and safety.
It is important to note that compliance with industry regulations and standards, such as those set by the Federal Aviation Administration (FAA), is a crucial consideration in structural design. The design must meet the necessary criteria for certification and undergo rigorous testing to ensure its safety and reliability.
Collaboration between structural engineers, aerodynamicists, and other design experts is key to achieving an optimal structural design. The team must consider the complex interactions between aerodynamics, weight distribution, and structural integrity to create a design that meets both performance and safety requirements.
By carefully determining the structural design, engineers can create an aircraft that not only performs well but also prioritizes safety, durability, and resilience under various operating conditions.
Step 7: Select Suitable Materials
In step 7 of the aircraft design process, selecting suitable materials plays a crucial role in ensuring the performance, durability, and safety of the aircraft. The choice of materials impacts factors such as weight, strength, corrosion resistance, and cost.
When selecting materials for aircraft construction, engineers consider a variety of factors, including the intended use of the aircraft, regulatory requirements, and industry best practices. Common materials used in aircraft manufacturing include:
- Aluminum Alloys: Aluminum alloys are widely used in aircraft construction due to their high strength-to-weight ratio and excellent corrosion resistance. They are commonly used in the construction of the fuselage, wings, and other structural components.
- Composite Materials: Composite materials, such as carbon fiber-reinforced polymers (CFRP), offer excellent strength-to-weight ratios and fatigue resistance. They are used in areas where high strength and light weight are critical, such as in wing structures and control surfaces.
- Titanium Alloys: Titanium alloys are known for their corrosion resistance, high strength, and high-temperature performance. They are often used in critical components such as landing gear, engine parts, and structural elements.
- Steel Alloys: Steel alloys are utilized in areas that require high strength and durability, such as landing gear and engine components. They provide excellent resilience and resistance to deformation under heavy loads.
The selection of materials is not solely based on their mechanical properties. Other considerations include factors such as cost, availability, manufacturability, and maintenance requirements.
Additionally, aircraft designers must consider the compatibility of different materials used in the construction of the aircraft. Different materials may have different coefficients of thermal expansion and other properties that can affect the integrity of the structure. Compatibility is crucial to avoid adverse reactions or structural instabilities.
It is important to comply with industry regulations and standards, which may dictate the specific materials and manufacturing processes that must be used. Certification authorities, such as the FAA, have guidelines and requirements regarding material selection to ensure the safety and airworthiness of the aircraft.
Collaboration between material scientists, engineers, and manufacturers is essential during this step. The expertise of material scientists can guide the selection process, taking into account factors such as material properties, availability, and cost-effectiveness.
By selecting suitable materials that meet the specific requirements of the aircraft design, engineers can ensure the structural integrity, performance, and longevity of the aircraft.
Step 8: Design the Wing Configuration
In step 8 of the aircraft design process, the focus is on designing the wing configuration. The wing is one of the most critical components of an aircraft as it directly influences its flight performance, stability, and efficiency.
Designing the wing configuration involves determining the shape, size, and placement of the wings on the fuselage. The wing design must take into account factors such as lift, drag, maneuverability, stability, and fuel efficiency.
One important consideration in wing design is the choice of wing shape. The most common wing shapes used in aircraft design include straight wings, swept wings, and delta wings. The selection of the wing shape depends on various factors, including the intended use of the aircraft, desired flight characteristics, and performance requirements.
The wing span and aspect ratio are also crucial parameters to consider. The wing span refers to the length of the wing from tip to tip, while the aspect ratio compares the wing’s span to its average chord length. Higher aspect ratios generally lead to improved lift efficiency but may also increase structural complexities.
Other factors to consider in wing configuration include the wing’s dihedral angle (the angle between the wing and the horizontal plane), the wing’s thickness and taper ratio, and the wing’s airfoil profile. Each of these factors affects the aerodynamic performance, stability, and control characteristics of the aircraft.
During the wing design process, engineers also need to consider the placement and integration of wing-mounted components. These components include fuel tanks, landing gear attachments, winglets (vertical extensions at the wingtips), and control surfaces such as flaps and ailerons.
Computer-aided design (CAD) tools and computational fluid dynamics (CFD) simulations play a crucial role in wing design. These tools allow engineers to analyze the airflow patterns, lift distribution, and aerodynamic forces acting on the wing. They help optimize the wing design for maximum efficiency and stability.
Collaboration between aerodynamicists, structural engineers, and other design experts is essential during the wing design process. Their expertise ensures that the wing design is not only aerodynamically efficient but also structurally sound and meets all safety requirements.
By designing the wing configuration carefully, engineers can create an aircraft that exhibits excellent lift characteristics, stability, maneuverability, and fuel efficiency, contributing to its overall performance and safety.
Step 9: Develop Landing Gear System
In step 9 of the aircraft design process, the focus is on developing the landing gear system. The landing gear plays a critical role in safely supporting and stabilizing the aircraft during takeoff, landing, and ground operations.
The development of the landing gear system involves determining the type of landing gear configuration that best suits the aircraft’s intended use and design objectives. Common types of landing gear configurations include tricycle, conventional (taildragger), tandem, or multi-wheel arrangements.
Factors that influence the landing gear configuration selection include the aircraft’s size, weight, intended runway types, operational requirements, and passenger comfort. For example, commercial airliners typically have retractable tricycle landing gear for improved ground stability and cabin space.
The design of the landing gear system must consider various components, including the landing gear struts, wheels, tires, brakes, shock absorbers, and retraction mechanisms. The system must be able to withstand the stresses of landing impact, provide effective shock absorption, and allow for safe ground maneuvers.
Additionally, the landing gear system must be designed to support the weight of the aircraft during touchdown and taxiing, distribute the load evenly across all landing gear units, and ensure proper clearance between the aircraft structure and the ground.
The structural design of the landing gear must also account for various operational conditions, like uneven terrain, crosswinds, and emergency landings. It is important to ensure that the landing gear system can withstand these challenging conditions without compromising the safety of the aircraft and its occupants.
The development of the landing gear system should also consider regulatory requirements and industry standards. Compliance with safety regulations and certification standards, set by organizations like the FAA, is essential to ensure the airworthiness and reliability of the landing gear system.
Collaboration between landing gear designers, structural engineers, and other relevant stakeholders is crucial during this step. Close coordination ensures that the landing gear system is integrated effectively within the overall aircraft design while meeting weight, strength, and safety requirements.
Through careful development and design, engineers can create a landing gear system that provides the necessary support, stability, and safety for the aircraft during all phases of operation.
Step 10: Consider the Cockpit and Interior Design
In step 10 of the aircraft design process, the focus shifts to considering the cockpit and interior design. This step involves creating a functional and ergonomic cockpit layout and designing a comfortable and user-friendly cabin for passengers and crew.
The cockpit design is crucial as it directly impacts the pilot’s ability to operate the aircraft safely and efficiently. Factors such as instrument placement, control interfaces, and visibility must be carefully considered. The goal is to create a cockpit that allows pilots to monitor critical flight information, access controls easily, and maintain situational awareness.
Ergonomics plays a significant role in cockpit design. Control panels, switches, and displays must be positioned in a way that minimizes pilot fatigue and ensures smooth and intuitive operation. Human factors considerations, such as reachability, visibility, and ease of use, are crucial in creating a cockpit design that enhances pilot performance.
When it comes to the cabin interior, passenger comfort and convenience take center stage. The layout should ensure adequate legroom, comfortable seating, and sufficient storage space for carry-on luggage. Considerations such as lighting, soundproofing, and climate control help enhance the overall passenger experience.
Interior design also involves selecting materials, fabrics, and finishes that are aesthetically appealing, durable, and easy to maintain. The choice of colors, textures, and patterns can contribute to the ambiance and atmosphere of the cabin.
The design of the cabin should also consider accessibility, especially for passengers with disabilities. Design features such as wider aisles, accessible lavatories, and adjustable seating can enhance the travel experience for all passengers.
Collaboration between cockpit designers, interior designers, and other stakeholders is crucial during this step. By considering the needs and preferences of pilots, crew, and passengers, the design team can create a cockpit and cabin that meet both functional and aesthetic requirements.
Ultimately, designing the cockpit and interior is about creating a space that enhances the overall experience and safety for both pilots and passengers. A well-thought-out and ergonomic design ensures optimal comfort, functionality, and satisfaction during the flight.
Step 11: Incorporate Safety Features
In step 11 of the aircraft design process, the focus is on incorporating safety features that prioritize the well-being of passengers, crew, and the aircraft as a whole. Safety is paramount in aviation, and designing an aircraft with robust safety measures is of utmost importance.
One key aspect of incorporating safety features is ensuring compliance with regulatory requirements and industry standards. Organizations such as the Federal Aviation Administration (FAA) set guidelines and regulations that govern aircraft safety. These regulations cover a wide range of aspects, including fire protection, emergency exits, crashworthiness, and the use of safety equipment.
Fire protection is a critical consideration in aircraft design. The inclusion of fire suppression systems, fire-resistant materials, and proper ventilation can greatly enhance the safety of the aircraft and its occupants in the event of a fire emergency.
Emergency exits are designed to allow for swift evacuation in case of a crisis. Their positioning, size, and ease of use are carefully planned to ensure effective evacuation and minimize the risk of congestion or delay during an emergency situation.
Crashworthiness focuses on designing the structure of the aircraft to withstand crash forces and protect occupants in the event of a crash or hard landing. This includes incorporating features such as reinforced cabin structures, energy-absorbing materials, and seating that can withstand impact forces.
Ensuring proper use and availability of safety equipment, such as life vests, oxygen masks, and first aid kits, is also critical. The design should account for the storage and accessibility of these safety features, enabling quick and easy access in emergency situations.
Collaboration with experts in safety engineering and human factors is crucial during this step. Understanding human behavior, evacuation dynamics, and emergency response helps in the effective incorporation of safety features into the aircraft design.
System redundancy is another important consideration for safety. Implementing backup systems in critical components such as flight controls, avionics, and power systems can mitigate the risk of system failures and enhance the overall reliability of the aircraft.
Throughout the design process, engineers should consider potential hazards, conduct risk assessments, and develop contingency plans to address emergency scenarios. Simulations and testing are also crucial to evaluate the effectiveness of safety features and ensure their proper functionality.
By incorporating comprehensive safety features, aircraft designers can create an aircraft that prioritizes the well-being and security of passengers and crew, while promoting a culture of safety in the aviation industry.
Step 12: Perform Simulations and Testing
In step 12 of the aircraft design process, simulations and testing play a crucial role in validating the design and ensuring its performance, safety, and reliability. This step involves subjecting the aircraft design to various simulations, analyses, and physical tests to evaluate its behavior and characteristics under different conditions.
Computer-aided simulations allow engineers to model and simulate the performance of the aircraft in a virtual environment. Aerodynamic simulations, structural analysis, and flight dynamics simulations help evaluate factors such as lift, drag, stability, and control. These simulations provide valuable insights into the aircraft’s behavior and performance, allowing for design refinements and improvements.
Furthermore, computational fluid dynamics (CFD) simulations help analyze the airflow patterns around the aircraft, allowing designers to optimize the aerodynamic design for maximum efficiency and stability.
Structural analyses, such as finite element analysis (FEA), are used to evaluate the stress, strain, and load distribution on the aircraft’s structure. This helps ensure the structural integrity and safety of the design.
In addition to simulations, physical tests are conducted to validate the design and performance of the aircraft. This typically involves building prototypes or scale models for wind tunnel testing, structural load testing, and system-level testing.
Wind tunnel testing allows engineers to analyze the aerodynamic behavior of the aircraft in a controlled environment. It provides data on lift, drag, stability, and other aerodynamic characteristics, which can be compared to the simulated results.
Structural load testing involves subjecting the aircraft’s structure to simulated loads and stresses to ensure it is capable of withstanding the anticipated forces during flight. This testing helps validate the structural design and identify any potential weaknesses or areas for improvement.
System-level testing involves evaluating the performance and functionality of various systems, including avionics, electrical systems, hydraulics, and flight controls. This testing ensures that all systems are operating as intended and interacting correctly with one another.
Through simulations and testing, engineers can identify and address design flaws, optimize performance, and fine-tune the overall aircraft design. Iterative testing and refinement are conducted until the design meets all safety and performance requirements.
It is important to note that simulations and testing continue throughout the design process, providing valuable feedback and validation as the design evolves. Collaboration between engineers, designers, and test pilots is crucial for interpreting the results, identifying areas for improvement, and ensuring the design meets all regulatory and certification requirements.
By performing thorough simulations and testing, the aircraft design can be validated, optimized, and ultimately, certified for safe and reliable operation.
Step 13: Refine and Optimize the Design
In the final step of the aircraft design process, the focus is on refining and optimizing the design. This step involves incorporating feedback, making necessary adjustments, and fine-tuning the design to achieve the best possible performance, efficiency, and safety.
Throughout the design process, collaboration and communication between multidisciplinary teams are crucial. Feedback from engineers, aerodynamicists, test pilots, and other experts is invaluable in identifying areas for improvement and optimization.
One aspect of refining the design involves taking into consideration the feedback and results from simulations, tests, and analyses performed in the previous steps. Any design flaws, performance limitations, or safety concerns that are identified should be addressed and resolved with appropriate modifications.
Based on the feedback and test results, adjustments may be made to the wing configuration, structural design, materials used, powerplant selection, or control systems. Iterative refinements ensure that the design meets performance objectives, adheres to safety standards, and incorporates the latest technological advancements.
During this phase, designers also optimize the design by focusing on factors such as weight reduction, fuel efficiency, and operational costs. By incorporating lightweight materials, streamlining the aerodynamics, and fine-tuning systems and components, engineers can optimize the aircraft’s performance and operational efficiency.
Moreover, advancements in technology or regulatory standards may occur during the design process. Designers should stay updated on these developments to ensure compliance and incorporate improvements or innovations that enhance the aircraft’s capabilities.
Computer-aided design (CAD) software and advanced modeling techniques assist in visualizing and optimizing the design. These tools enable designers to analyze and assess different design alternatives, allowing for informed decisions and optimizations.
Another critical aspect of the refinement process is cost optimization. Designers carefully evaluate the manufacturing processes, assembly procedures, and maintenance requirements to minimize both manufacturing and operational costs without compromising safety or quality.
Lastly, the refinement phase includes evaluating the overall aesthetics and branding of the aircraft. Visual elements such as exterior paint scheme, logo placement, and interior decor contribute to the overall identity and market appeal of the aircraft.
By continuously refining and optimizing the design, engineers can ensure that the final aircraft design is a well-balanced, high-performance, and safe product that meets the needs of its intended users and operators.
Conclusion
The process of designing an aircraft is a complex and intricate journey that requires careful consideration, expertise, and collaboration. Each step in the design process plays a crucial role in creating an aircraft that meets performance objectives, safety standards, and customer expectations.
From defining the design objectives to performing simulations and testing, and finally refining and optimizing the design, every stage contributes to the overall success of the aircraft design. Through research, analysis, and collaboration with experts, engineers can create an aircraft that is innovative, efficient, and safe.
The integration of aerodynamics, structural design, material selection, and safety features ensures the aircraft’s performance, durability, and reliability. Attention to detail in areas such as the cockpit and interior design enhances the comfort, functionality, and user experience.
Throughout the design process, the emphasis is not only on meeting regulatory requirements and industry standards but also on pushing boundaries and embracing technological advancements. This leads to continuous improvement and innovation in the aviation industry.
It is important to note that the aircraft design process is not a linear path, but rather an iterative and collaborative journey. Feedback, adjustments, and refinements are integral to achieving a successful and optimal design.
In conclusion, designing an aircraft is an intricate blend of science, engineering, creativity, and innovation. By following the step-by-step process outlined in this article and leveraging the expertise of a multidisciplinary team, engineers can create aircraft that are not only visually appealing but also perform exceptionally well in terms of aerodynamics, structural integrity, safety, comfort, and efficiency.
The aircraft design process is ever-evolving, striving to meet the evolving needs of the aviation industry. It is through dedication, ingenuity, and a commitment to excellence that engineers continue to shape the future of flight with their remarkable designs.